Utveckling av industriellt underhåll från ursprung till nutid
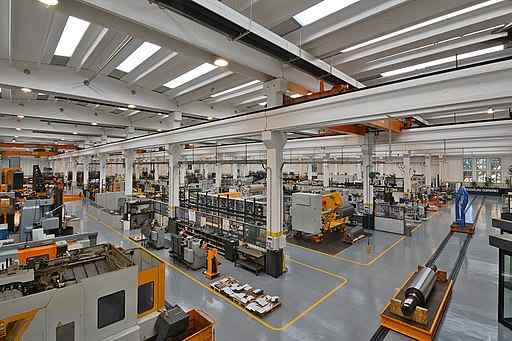
- 2196
- 586
- Prof. Erik Johansson
De Industriellt underhållsutveckling Det började vara mer betydelsefullt efter det första från första världskriget, där maskinerna var tvungna att arbeta med maximal kapacitet och utan avbrott. Tidigare var arbetet den som utförde nästan 90% av arbetet, jämfört med de 10% uppskattade att de gjorde de första maskinerna.
Industriellt underhåll härstammar samtidigt som maskiner började implementeras för produktion av varor och tjänster, i början av 1800 -talet. Som en gemensam egenskap för alla dess utvecklingsfaser presenteras behovet av att göra det alltmer specialiserat.
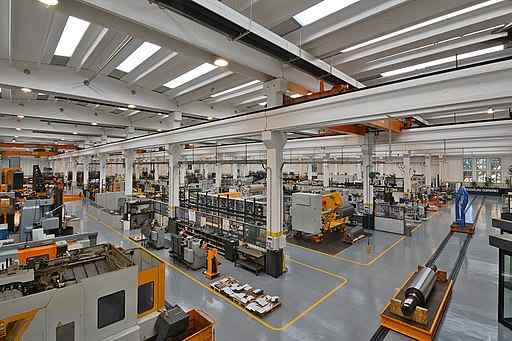
Industriellt underhåll är den uppsättningen av organisatoriska tekniska åtgärder, som tidigare kan utarbetas, som syftar till att upprätthålla utrustningens funktionalitet och garantera ett optimalt tillstånd av maskiner över tid.
Bland de industriella underhållsmålen kan nämnas: bevara arbetsförmågan för maskinerna, minska oförutsedda stopp, bidra till ökningen av produktiviteten, bevara i perfekt skick produktionsmedel med en lägsta kostnad.
Genom industriella underhållsplaner är det avsett för ditt livslängd.
Industriella underhållsuppgifter är inte exklusiva för utrustning och maskiner, utan för fast eller mobil installation, industriella, kommersiella eller specifika tjänster, det vill säga alla typer av produktiva goda.
[TOC]
Steg från sitt ursprung till nutid
Första generationen: Från den industriella revolutionen till 1950
Den motsvarar Totalt korrigerande underhåll, där viss nedbrytning förväntas fortsätta med respektive ersättning. Denna fas identifieras vanligtvis före 1950 och är den längsta scenen eftersom den börjar med den industriella revolutionen. Underhållskostnader brukade vara ganska höga och arbetslöshetstiden för att lösa problemen förlängdes.
Med genomförandet av serieproduktionen, efter första världskriget, började fabrikerna att upprätta minimala produktionsprogram och behovet av att bilda en utrustning som koncentrerades på att upprätthålla maskinerna i produktionslinjerna och minskar till bokstaven möjlig tid stoppet stopp.
Kan tjäna dig: industriell automatiseringParallellt med produktionsområdet sedan underhållet som var inriktat på att reparera korrigerande eller brådskande fel. Dessutom tilldelades förebyggande uppgifter att undvika fel.
Korrigerande underhåll kännetecknades av att presentera höga arbetskraftskostnader och höga möjlighetskostnader, eftersom tillgången på reservdelen bör vara omedelbar för att kunna hantera eventuella skador som registrerades.
Bland de mest uppenbara nackdelarna är kvalitetseffekt på grund av utrustningens progressiva slitage, risken för att inte ha den ersättningsansökan vilket innebar stora kostnader, tider dödade av plötsliga misslyckanden och risker att andra problem kunde genereras parallellt.
Andra generationen: Från 1950 till 1970
Förebyggande underhållsarbete var redan systematiserat för tillkomsten av andra världskriget. Och några år senare uppstod American Quality Control Society, som hjälpte till att genomföra den statistiska studien av arbetet, vilket också förbättrade kvaliteten på de produkter som erhållits.
Den andra generationen fokuserar på Förebyggande underhåll av nedbrytningar, så cykliska och repetitiva verk utförs med en viss frekvens för att uppnå nämnda mål. Denna fas sträcker sig till slutet av 70 -talet.
I den börjar förebyggande ersättningar göras, eftersom förhållandet mellan utrustningens livstid och deras sannolikhet för misslyckande upptäcks.
Förebyggande underhåll har flera metoder: det kan vara en process som ska genomföras regelbundet, i allmänhet med ett tidsintervall på 6 till 12 månader. Det kan också planeras enligt tillverkare eller enligt de standarder som fastställts av Engineering.
En annan modalitet kan tänka sig att implementera förbättringar i processen och även om den inte har en etablerad frekvens är det en omdesign att optimera processen. Slutligen sker det autonomt underhåll som utförs av operatören med enkla aktiviteter eller rutin.
Tredje generationen: Från 1980 till 1990
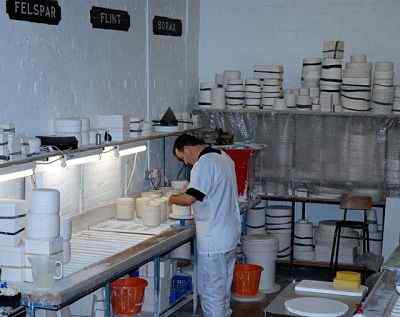
Underhåll implementeras på villkor, det vill säga den som beror på övervakning av parametrar beroende på vilken ersättning eller renovering av maskiner kommer att genomföras.
Kan tjäna dig: Telegraph: Historia, uppfinningen, evolution, hur fungerarDetta arbete möjliggörs tack vare tillgängligheten av tillförlitlig inspektions- och kontrollutrustning, som gör det möjligt att känna till utrustningens verkliga tillstånd genom periodiska mätningar.
Det är tiden för Förutsägbart underhåll, som bestod av tidig upptäckt av begynnande symtom på framtida problem. Orsakseffektstudier utförs vanligtvis för att ta reda på ursprunget till misslyckanden. Ett differentierande element i detta skede är att de börjar engagera sig i produktionsområdena i upptäckt av problem.
En av de stora fördelarna med förutsägbart underhåll är möjligheten att övervaka och registrera fel, så det blir lättare att schemalägga framtida reparationer och mindre ingripanden för underhållspersonal kommer att registreras.
Fjärde generationen: Från 1990 till idag
Början av denna fas identifieras vanligtvis på 90 -talet när amerikanska företag redan hade införlivat i sin dynamik begreppet total kvalitet som japanska industrier hade främjat från 60. Total Quality Management (TQM) försökte skapa kvalitetsmedvetenhet i alla organisationens processer och de människor som arbetade med den.
Den fjärde generationen motsvarar Totalt produktivt underhåll vilket är inspirerat av den filosofin om japanskt ursprung som söker excellens eller sagt i en fras: få maximalt med acceptabel kvalitet, åtminstone möjliga kostnader, i pärl- och omfattande mening. För detta utförs små underhållsuppgifter som justering, inspektion, ersättning av delar och kontinuerlig interaktion med underhållshanteraren.
Programmet fokuserade på den mänskliga faktorn i hela företaget som förebyggande underhållsuppgifter tilldelas för att maximera varornaets effektivitet. Det antar tre principer: Håll alltid anläggningarna i gott skick, fokusera på att öka produktiviteten och involvera personalens helhet.
Detta är fasen av kontinuerliga förbättringssystem och kännetecknas av genomförandet av åtgärder för förbättring och övervakning av åtgärder. Underhåll blir en fördel, snarare än en nödvändig ondska, och antas som ett åtagande av alla avdelningar i organisationen.
Målet är att uppnå den totala effektiviteten hos utrustningen som innebär ekonomisk effektivitet genom tillgänglighet, maximal prestanda och kvalitetsprodukter.
Det kan tjäna dig: Human-Machine System: Egenskaper och exempelDessutom implementeras vanligtvis tre andra verktyg: riskteknik som innebär att bestämma konsekvenser av misslyckanden som är acceptabla eller inte; tillförlitlighetsanalysen som hänvisar till att identifiera genomförbara och lönsamma förebyggande uppgifter; förbättringen av underhållbarhet som består av att minska tiderna och underhållskostnaderna.
I detta skede har det skett viktiga förändringar i lagstiftningen om säkerhet och hygien på jobbet, liksom mer vänliga metoder för miljön. Därför började rena enheter, extraktionsanläggningar, brusdämpning, detekteringsutrustning, kontroll och larm att implementeras.
Idag uppskattar experter på fältet att underhållskostnader kommer att drabbas av en progressiv ökning som kommer att leda industrier för att generera mer pålitliga och enkla underhållsprodukter.
Betydelse av underhåll
Industriellt underhåll gick från att vara en nödvändig ondska som flera avdelningar i en organisation är engagerade och involverade. Detta beror i princip på grund av att den verkliga betydelsen av effektiv hantering av fel eller problem med utrustning och anläggningar har erkänts, vilket kan påverka någon av stadierna för produktion av varor eller tjänster.
Det bör noteras att vikten av industriellt underhåll ligger i följande:
- Förhindrar arbetsolyckor och ökar säkerheten för människor.
- Minskar förluster på grund av produktionsstopp.
- Svårighetsgraden av de misslyckanden som inte undviks minskar.
- Förhindrar skador som kan vara oåterkalleliga i utrustning eller anläggningar.
- Garanterar utrustningens acceptabla prestanda.
- Tillåter att dokumentera nödvändiga underhållsprocesser för varje maskin.
- Förlänger livslängden för utrustning eller varor.
- Behåller produktiva varor i säkra och förutbestämda driftsförhållanden.
- Förbättrar aktivitetens kvalitet.
- Tillåter korrekt förberedelse av budgeten, anpassad till företagets behov.
Referenser
- Muñoz Abella, m. (2003) Industriellt underhåll. Madrid: Carlos III University of Madrid. Maskinteknik.
- Mora Gutiérrez, a. (2009). Underhåll: Planering, exekvering och kontroll. Mexiko: Alfaomega Grupo -redaktör.
- Industriellt underhåll. (s.F.). Återhämtat sig från eucured.Cu
- Barnbarn. Underhållshistorik. (2009, 27 maj). Hämtad från industriellt underhåll2009.Bloggfläck
- Villada, "Underhåll som en konkurrensstrategi", Rev. Fak. Yttre. Univ. Antioquia, nej. 17, sid. 7-13, 1998.
- Utvecklingen av industriellt underhåll: Blogg: ATS. (2019, 26 juli). Återhämtat sig från AdvancedTech.com
- « Natriumnitrat (nano3) struktur, egenskaper, användningar, risker
- Euklidiskt avståndskoncept, formel, beräkning, exempel »